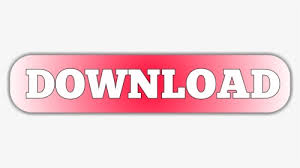
When choosing a die, factors that will affect the CLR you choose include the material type and grade to be bent, wall thickness, the OD, the application or design of the end product, and overall appearance required. If you’re having trouble translating that last sentence into English, check out the picture above. Using the image below, you can see how the radius of a bend has a significant impact on the resulting part. CLR is the distance from the center of curvature to the centerline (axis) of the pipe. When referring to the radius of a die, we are referring to the center-line radius (CLR) that results from bending. USE THIS DIAGRAM AS A REFERENCE WHILE YOU LEARN TUBE AND PIPE BENDING BASICS If you need additional assistance, don't hesitate to give Pro-Tools a call and our team will be happy to help you. Click here for more information on this and other Swagelok Essentials Training classes, as well as our schedule of upcoming training dates.To get started bending tube or pipe in your shop, Pro-Tools has put together these basic metal fabrication terms to make beginning your first bending experience as easy as possible. Benefits include: reduced installation time, less wastage, improved flow, eliminated leak points and increased safety. The course is designed to simulate real-world applications and troubleshoot actual scenarios encountered in the field.
#Instrument tube bending install#
Students will work through multiple practical examples to measure, cut, bend, and install tubing into a pre-fabricated instrument panel. The Swagelok Tube Bending Essentials course offers foundational knowledge needed to introduce bent tubing to your system to eliminate connections and leak points found in traditional threaded or welded pipe systems. More connections means greater potential for leaks.
Bend the tube 45 degrees as described in the tech tip video. This will help ensure the bend is made in the intended direction. Place a directional mark over the bend mark to indicate the outside, or heel, of the 45 degree bend. Make a second bend mark four inches from the vertex of the 90 degree bend, away from the reference mark. Bend the tube 90 degrees as described in the tech tip video. Measure four inches from the reference mark and make a bend mark to indicate the first desired bend length. Place a reference mark at the end of the tube from which you are beginning the measurements. It generally requires less math, is faster, and is more adaptable to multiple runs of tubing: The measure-bend method is the preferred tube bending procedure, and is taught in our Tube Bending Essentials training course. The tech tip video below covers the basics of tubing selection, as well as operation of our hand tube bender and procedure for completing two single bends with a measured degree of separation. Have a small project or difficulty justifying a capital expenditure for equipment purchase? We also offer equipment rentals, including tube bending equipment, to meet your needs. Our hand tube benders are appropriate for smaller, instrument tubing applications (up to ½ inch OD), while our bench top bender and electric tube bender handle tubing sizes up to four inch OD. Depending on your application, Swagelok has the tools you need. They’re robust and reduce installation time and effort, as well as the potential for wrinkling or other damage to the tubing during bending. In terms of value and performance, Swagelok Tube Benders lead the industry. Tube bends also produce better flow characteristics based on the smooth internal surfaces reducing flow losses and drag, as well as contributing to reduced pressure drop and turbulence, all while increasing system performance. By economizing expenses related to additional fittings and connection points, not only material costs but also procurement, storage and labour costs can be significantly reduced. Tube bending has many benefits in terms of cost effectiveness, production and system performance. The incorporation of tube bends in fluid system design is important from many different perspectives – procurement, installation and performance. Modern processes are pushing pressure, flow, and temperature requirements to new heights every day, yet the basic concepts of system design have not changed over the years. Leaks that were once considered nuisances are now classified as fugitive emissions and hazardous spills, problems that can shut down plants. The demands placed on today’s fluid systems are much tougher than they were a decade ago. My Sales and Service Center: Swagelok Calgary. ABSA Certificate of Authorization Permit. Process Analyzer Sampling System Subsystem Training. Process Analyzer Sampling System Training. Sample System Problem Solving and Maintenance. Leak Detectors, Lubricants and Sealants.